Reinvention and industrial resilience
When the Covid-19 pandemic changed the course of “business as usual,” the Canal’s industrial workshops were among the first areas to redesign their work dynamics. Their resilience was key to keeping Canal operations reliable and consistent.
The Mechanics and Tracing workshop of the Panama Canal Industrial Division has machines that are unique in the world because of their specialty and size. The lathes are special designs for the Canal, and they manufacture parts with unique shapes. In this workshop, precision to the thousandth of a millimeter is achieved. In this small section of the Industrial Division, the permanent changes imposed by Covid-19 on the operation’s support services can be appreciated. Inside the large natural light galley that houses some of the workshops, gusts of sea breeze blow. Emerson Bermudez is the manager in charge of the Floating and Industrial Equipment Maintenance Section.
“Here we keep the floating equipment used in Canal transit operations in optimal working order, as well as the dredging equipment that provides maintenance to the waterway. We repair the gates and components of the Panamax locks, as well as the components of the water treatment plants, hydroelectric plants, thermoelectric plants and refrigeration plants,” says Bermúdez.
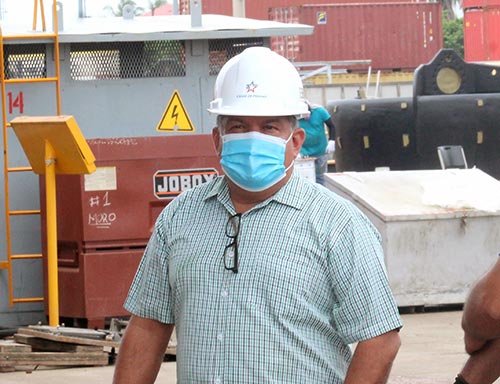
“La Industrial“, as it is known, has 15 workshops for almost all manual crafts. It has dry dock facilities, synchroelevator, docks and industrial workshops.
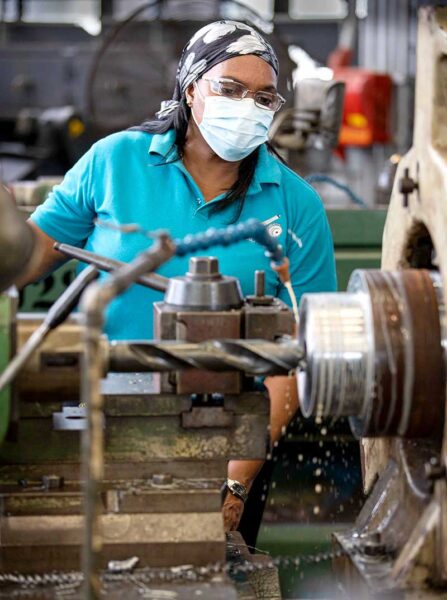
“La Industrial is like the emergency room of the Panama Canal. We are always looking for a timely solution. When a piece of equipment leaves here, we guarantee that it is in good working order,” says Amanda Spence, a lathe mechanic at the workshop.
Permanent change
“The main challenge was to work with employees who volunteered to attend and who followed all the biosecurity measures, even when they did not know much about the virus,” recalls the manager.
One of Industrial’s first actions was to collaborate with Idaan to repair and maintain the water pumps of the Federico Guardia Conte water treatment plant, at a time when hand washing was more important than ever.
“So far, we have rehabilitated five suction pumps, as well as provided the support of divers for specialized work inside the Chilibre plant,” says Bermúdez.
In this process, the creativity of the Canal workforce shines through. For example, the drinking water pumps had rubber rings to cushion the metal joints, but in the workshop, they considered that the high-density polyurethane of the Neopanamax locks fenders could provide better performance. This is a very high quality material that remains as a residue when the fenders are removed from the walls of the new locks that have already fulfilled their use.
“We electricians also do a lot of retrofitting with that material,” Spence adds, pointing to the reused yellow material.
This creativity and inventiveness of Canal artisans is legendary. On many occasions, when a part can’t be sourced, “we concentrate, sit down and see how we will resolve,” Spence says with a proud smile.
Constant machines
Sitting at his desk with his eyes fixed on a piece of steel, José Luis Martínez prepares to start a new project. “I’m taking the measurements to develop an idea from colleagues to modify the exhaust of the tugboats,” he points out on a blueprint.
Panama Canal tugboats are very powerful machines that perform essential work in the operation, due to their great maneuverability and power. They are the ones that pull and guide the ships that cross the interoceanic waterway. These floating craft receive scheduled maintenance.
“Here we offer fairing services (hull rehabilitation), reconditioning of main engines and routine maintenance to all tugboats,” Bermúdez points out.
106 years and more
Panama Canal locomotives have seen it all: war, peace, several epidemics and 21 years of Panamanian sovereign administration. From the first generation produced by General Electric to the current ones made by Mitsubishi, these strong machines are witnesses of the ups and downs of the maritime industry and the technological changes of the new century.
The Precision Mechanics workshop repairs the drive axles of the locomotives used on the original Canal.
“We give them preventive and corrective maintenance. They are sent to us already disassembled from Pedro Miguel and we change bushings, worn spacers, gears, and also the wheels,” explains Efraín Rivera, a graduate of the Colegio Artes y Oficios.
“The worst thing about Covid-19 was that when I got sick, my whole family got infected. My son told me that he got scared for me,” Rivera says of his experience with the virus.
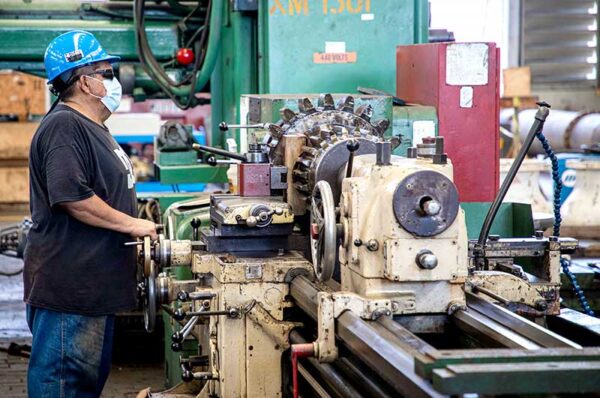
“When I came back, I was checked by the office doctor and he told me I was fine; that gave me peace of mind,” he recalls. Bermudez sums up the lessons of this period as follows: “Losing a colleague is like losing a brother. That is why the pandemic has taught us to take care of ourselves and our colleagues. We are a family, since many of us have spent a lifetime working together”.
Similarly, José Luis Martínez adds that the hardest part of this period was losing co-workers to Covid-19. “Some of them went in with me (to work), it was very hard,” he says with his voice cracking. In this small part of the Industrial live the changes that the pandemic has imposed on the entire planet, but the attitude is the first defensive measure. “Coming back was a challenge, but we are used to challenges. And we are also used to changes,” Rivera says serenely.
The “La Industrial” Workshops
– Vessel assembly
– Welding
– Pipe Assemblers
– Tinsmithing5
– Electricity
– Carpentry
– Precision Mechanics Workshop
– Naval Mechanics Workshop
– Diesel engine workshop
– Painting and coatings
– Industrial
– Rigging and Cranes
– Gates and Spillways
– Diving School
– Atlantic Boat Workshop
– Pacific Boat Shop